CFD para equipamentos de combustão: ferramenta visual para diagnósticos avançados
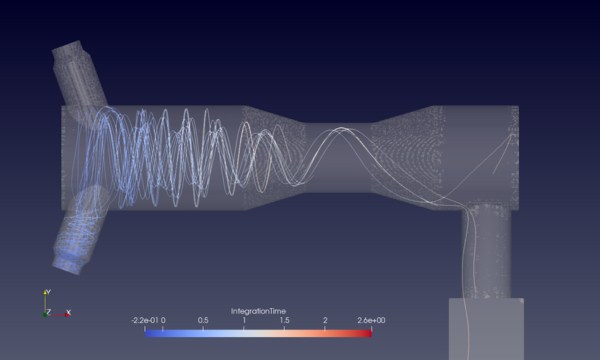
Antes de alterar a carga em um equipamento de incineração, é fundamental prever como o novo escoamento se comportará internamente. Desviar-se da condição projetada pelo fabricante pode resultar em falhas operacionais de difícil diagnóstico, impactando equipamentos aparentemente independentes e, muitas vezes, com efeitos que surgem meses após a modificação. Para evitar isso, a análise do sistema como um todo, utilizando ferramentas avançadas como o CFD, se torna essencial. Isso permite antecipar possíveis falhas ou, quando já manifestadas, orientar as equipes na solução do problema. O Problema: falhas interligadas em um incinerador de organoclorados A modificação do balanço de resíduo entre os queimadores de um incinerador de organoclorados resultou em uma série de falhas inesperadas em equipamentos a jusante. Cada parada do sistema de incineração gerava a necessidade de uma parada completa da usina, acarretando prejuízos milionários. As falhas eram tratadas de forma isolada, resultando em ações corretivas dispersas e ineficazes. Após anos de tentativas da equipe de manutenção — algumas bem-sucedidas, outras não —, a substituição completa do sistema parecia ser a única saída. Como alternativa, a Figener foi contratada para conduzir um diagnóstico avançado de todo o sistema de incineração. O trabalho incluiu visitas à unidade, inspeções internas nos equipamentos, modelagens de processo e simulações computacionais (CFD) para entender as causas das falhas. Dentre os vários problemas encontrados, destacamos a falha na parede refratária próxima aos queimadores. Inicialmente, o cliente associou o problema a uma escolha inadequada do material refratário e, por isso, decidiu substituí-lo. Embora essa troca tenha trazido melhorias pontuais, o problema persistiu, evidenciando a necessidade de uma investigação mais profunda. Imagem 1: Queda da parte refratária próxima à pré-câmara de combustão de um dos queimadores. Etapas do Estudo 1. Modelagem da combustão Simular a combustão via CFD é um desafio técnico, especialmente pela ausência de mecanismos de reação definidos para todas as interações químicas reais. No caso em estudo, o composto incinerado não possuía uma fórmula química fixa, exigindo a modelagem e validação de um mecanismo de reação simplificado. Essa etapa foi crucial para garantir a representatividade e a confiabilidade dos resultados. 2. Separação do problema em sub-regiões Estudar o incinerador inteiro com um nível elevado de detalhes seria inviável devido à complexidade geométrica e ao tempo de processamento necessário. Para contornar essa limitação, a Figener dividiu o sistema em sub-regiões. A primeira parte do estudo focou no comportamento inicial da combustão na região do queimador. Simulando esta área isoladamente, foi possível entender a dinâmica inicial de mistura das correntes participantes da combustão. Isso permitiu reduzir a necessidade de detalhamento geométrico na simulação completa, acelerando o processo sem perder a precisão técnica. Imagem 2: Sub-região focada na área do queimador. 3. Simulação do incinerador completo Com as condições de contorno devidamente ajustadas a partir do estudo da sub-região, a Figener prosseguiu com a simulação integral do incinerador. Isso incluiu a modelagem de reações químicas e a representação completa dos queimadores no domínio de cálculo. Imagem 3: Corte do domínio completo da simulação. 4. Identificação do problema e proposta de mitigação A análise do sistema completo confirmou uma das principais suspeitas da Figener: a geometria do incinerador causava o desvio da chama de um dos queimadores para cima, fazendo com que ela atingisse o refratário. Essa condição indesejada provocava trincas e quedas do material refratário em poucas semanas de operação. Para mitigar o problema, a Figener testou soluções como o redimensionamento dos queimadores e a alteração da inclinação. Além disso, as análises de CFD possibilitaram uma correlação entre a falha no refratário e outras falhas encontradas ao longo do sistema. Imagem 4: Linhas de corrente destacando o tempo de residência — parâmetro importante no processo de incineração. Além disso, problemas extras foram identificados, incluindo: Impactos positivos para o cliente O estudo liderado pela Figener trouxe ganhos significativos para o cliente, indo além da identificação de falhas. A análise do sistema de incineração de forma integrada permitiu: Por que escolher a Figener? Com mais de 30 anos de experiência e uma equipe altamente qualificada, a Figener é especialista em análises técnicas avançadas que transformam desafios complexos em soluções práticas. Nossas ferramentas de simulação computacional e metodologias personalizadas garantem resultados precisos e confiáveis, ajudando empresas a aumentar a eficiência operacional e a sustentabilidade de seus projetos. Traga seus projetos para o próximo nível! Antes de aprovar novos layouts para sua usina, consulte a Figener! 📩 contato@figener.com.brDescubra como nossos estudos de CFD podem transformar a eficiência e a segurança de seus projetos.
CFD para cenários de falha: testar e dimensionar dispositivos de segurança com agilidade
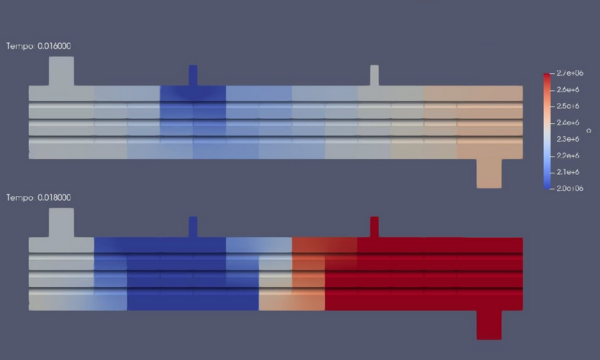
Dispositivos de proteção contra surto de pressão são exigidos por normas de segurança em determinados equipamentos. No entanto, os cálculos necessários para o dimensionamento podem ser trabalhosos e suscetíveis a interpretações divergentes, comprometendo a operação. O uso de CFD (Computational Fluid Dynamics) permite analisar o comportamento do surto de pressão em tanques pressurizados, avaliando a evolução temporal da onda de pressão e auxiliando na seleção e no dimensionamento dos dispositivos de proteção mais adequados. O Problema: selecionar, de forma econômica, rápida e segura, o tipo e o número de dispositivos de proteção contra surto de pressão No projeto de trocadores de calor para aquecimento de gás natural, a norma API 521 exige o dimensionamento do sistema de proteção para cenários de falha, como o rompimento do tubo de gás no interior do casco. Esse processo envolve diversas variáveis, o que gera uma série de dúvidas: Embora a lógica inicial sugira que mais dispositivos significam maior segurança, na prática, o excesso de dispositivos pode não ser eficaz. A análise precisa considerar múltiplos fatores simultâneos, como: A complexidade do problema e a importância da aplicação exigem análises precisas e sofisticadas, especialmente em cenários onde a escolha de dispositivos inadequados pode resultar em soluções caras e ineficazes. Etapas da Análise Para isso, foi necessário customizar o software OpenFOAM, o que permitiu à equipe da Figener implementar ajustes específicos para o estudo. Essa personalização foi essencial para tornar a simulação viável e robusta. Foram simuladas diferentes condições de gatilho, atraso de ativação e capacidade de vazão de cada tipo de dispositivo. Além disso, a Figener testou o impacto da posição e quantidade de dispositivos, identificando a configuração mais eficaz. Figura 1 – Pressão máxima dentro do vaso durante o transiente, para diferentes cenários Figura 2 – Evolução da pressão dentro do trocador de calor Solução Otimizada para Atender à Norma O uso de CFD permitiu que diversas alternativas fossem testadas, trazendo uma análise precisa e visual do comportamento do sistema. Isso viabilizou o dimensionamento correto e eficiente dos dispositivos de proteção, com impacto positivo na segurança e na economia do projeto. Sem o uso de CFD, o cenário economicamente mais viável dificilmente seria identificado. Por que escolher a Figener? Com mais de 30 anos de experiência e uma equipe altamente qualificada, a Figener é especialista em análises técnicas avançadas que transformam desafios complexos em soluções práticas. Nossas ferramentas e metodologias personalizadas garantem resultados precisos e confiáveis, ajudando empresas a aumentar sua produtividade. Antes de aprovar novos layouts para sua usina, consulte a Figener em contato@figener.com.br e descubra como nossos estudos em CFD podem fazer a diferença na eficiência e na sustentabilidade de seus projetos.
CFD para Torres de Resfriamento: Otimize o posicionamento e Evite Perdas Operacionais
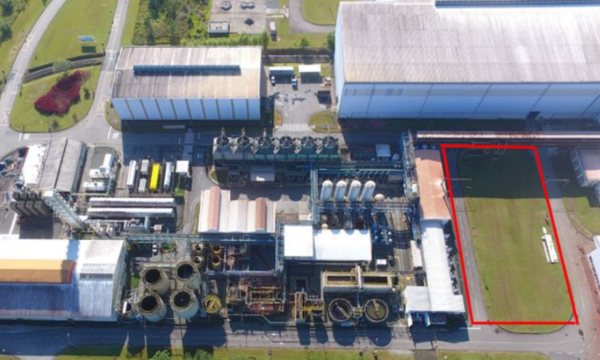
Ao expandir a área de utilidades de uma unidade fabril, é essencial considerar como os equipamentos existentes podem impactar a operação de novos componentes. Isso é particularmente crítico no caso de torres de resfriamento, que dependem da qualidade do ar admitido para operar com máxima eficiência. A interação entre torres próximas, somada a condições ambientais específicas, pode comprometer significativamente o desempenho do sistema. O Desafio: Influência da Umidade e do Layout no Desempenho Em um projeto recente, a Figener foi contratada para avaliar a viabilidade de instalar uma nova torre de resfriamento próxima a uma torre existente. O terreno, localizado próximo ao litoral e cercado por diversas edificações, apresentava condições desafiadoras devido à alta umidade e ao regime variável de ventos. A figura a seguir mostra uma foto da unidade, em que se observa à direita o terreno em que se deseja instalar novas torres de resfriamento. Figura 1 – Área para nova torre de resfriamento O principal objetivo era entender como a pluma de exaustão da torre existente poderia afetar a eficiência da nova torre, considerando diferentes cenários de vento e condições sazonais. Para isso, a Figener utilizou sua experiência em CFD (Computational Fluid Dynamics), modelando o ambiente e simulando múltiplos cenários. Etapas do Estudo com CFD Figura 2 – Vista superior do domínio e rosa dos ventos Figura 3 – Pluma colorida de acordo com a umidade relativa Figura 4 – Linhas de corrente coloridas conforme a umidade relativa, ilustrando o comportamento do fluxo de ar e da umidade em ventos fortes. Esses dados ajudaram a identificar condições críticas que poderiam comprometer o desempenho das torres e influenciaram diretamente a decisão sobre o posicionamento e o dimensionamento da nova instalação. Resultados e Impacto para o Cliente O estudo permitiu responder perguntas estratégicas: Com base nas simulações, a equipe do cliente conseguiu tomar decisões fundamentadas, evitando custos futuros e maximizando a eficiência operacional. Por que Escolher a Figener? Com mais de 30 anos de experiência e uma equipe altamente qualificada, a Figener é especialista em análises técnicas avançadas que transformam desafios complexos em soluções práticas. Nossas ferramentas e metodologias personalizadas garantem resultados precisos e confiáveis, ajudando empresas a aumentar sua produtividade. Antes de aprovar novos layouts para sua usina, consulte a Figener!📩 contato@figener.com.br Descubra como nossos estudos em CFD podem fazer a diferença na eficiência e sustentabilidade de seus projetos.
CFD em fornos de craqueamento: estudo avançado para otimizar o projeto de um reator
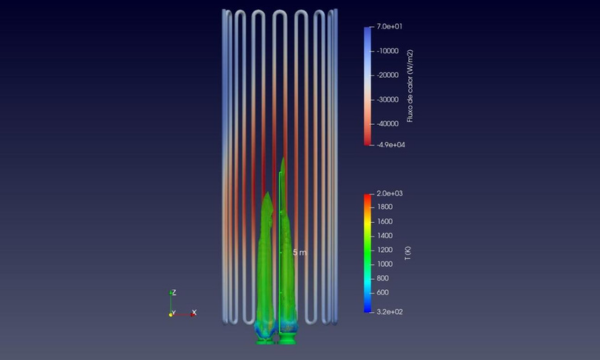
Um forno de craqueamento passava por paradas mais frequentes que o tempo de campanha esperado. O problema era formação de coque, por vezes localizado em um mesmo ponto, que gradualmente obstruia o reator levando ao aumento de pressão e consequente sua parada. Ademais, nas regiões de depósito, a temperatura de metal subia significativamente, trazendo riscos de integridade ao reator. Isso parava toda a unidade por alguns dias, pois exigia uma decoqueificação completa do reator, além de outros procedimentos de limpeza e testes. A cada dia parado, os custos são elevadíssimos, trazendo prejuízos enormes ao cliente. A Figener foi contratada para ajudar na investigação do problema, identificar formas de otimizar o consumo de combustível e aumentar o rendimento da unidade. O uso de CFD (Computational Fluid Dynamics) é extremamente vantajoso nesse caso, por permitir inúmeros testes em diferentes configurações, impossíveis de se testar em operação. O Problema: disposição dos queimadores em relação ao reator não era otimizada A reação de craqueamento em questão depende tanto da temperatura quanto do fluxo de calor, e o coque começa a se formar apenas a partir de certo ponto da reação, próximo do final do reator. Assim, balancear o fluxo de calor da chama com a região em que incide no reator (entre começo e final) é um caminho interessante a se explorar. Incluir a reação de formação do produto e do coque no modelo seria inviável na realidade industrial desse projeto. Assim, a Figener criou um modelo externo de avanço da reação que recebe o fluxo de calor resultante do CFD e determina a taxa de formação de coque no tempo. Figura: chama e fluxo de calor para o reator original Com esse cenário base calibrado para os dados reais, a Figener passou a testar diversas posições e combinações de queimadores, acompanhando sempre a evolução do coque. A solução: reposicionar o queimador e alterar o balanço de ar/gases Deslocar o queimador para perto da região de início da reação favorece fortemente o avanço da reação, permanecendo ainda fora da zona de formação de coque. Intervenções desse tipo são pouco ortodoxas, mas possíveis de testar com ferramentas computacionais. Figura: chama e fluxo de calor para o reator modificado A evolução do coque não trouxe preocupação, e a temperatura de metal – medida crítica para integridade do reator – permaneceu abaixo do caso de referência na previsão de 12 meses. Figura: evolução da temprratura de metal ao longo do reator após 1 ano de operação Compondo essa solução com modificações no fluxo de ar/combustível, recirculação de parte dos gases de combustão e adoção de pré-aquecedor de ar, economias superiores a 5% são esperadas para esse reator, considerando o produto por kg de combustível queimado. Impactos positivos para o cliente O estudo liderado pela Figener trouxe potencial de ganhos importantes para o cliente. A análise do problema acoplando o lado do forno com o do reator permitiu: Por que escolher a Figener? Com mais de 30 anos de experiência e uma equipe altamente qualificada, a Figener é especialista em análises técnicas avançadas que transformam desafios complexos em soluções práticas. Nossas ferramentas de simulação computacional e metodologias personalizadas garantem resultados precisos e confiáveis, ajudando empresas a aumentar a eficiência operacional e a sustentabilidade de seus projetos. Traga seus projetos para o próximo nível! Antes de aprovar novos layouts para sua usina, consulte a Figener! 📩 contato@figener.com.brDescubra como nossos estudos de CFD podem transformar a eficiência e a segurança de seus projetos.
CFD para diagnóstico em caldeiras: problemas muito além da baixa capacidade
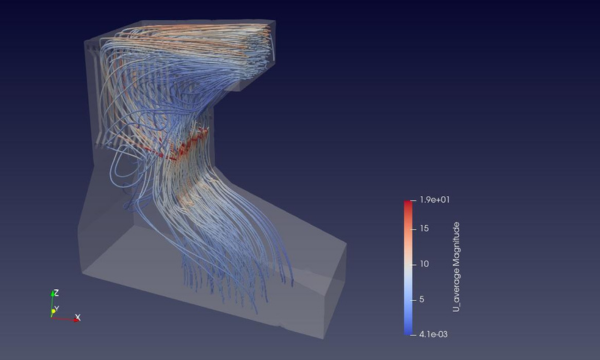
Uma caldeira flamotubular de 30MW à biomassa não conseguia alcançar sua plena carga, demandando paradas muito frequentes para limpeza do feixe convectivo. As incrustações formadas eram rígidas, incapazes de serem sopradas pelos sopradores de fuligem. As paradas da caldeira resultavam na interrupção do suprimento de vapor para o sistema de secagem, levando portanto à parada de toda a unidade. Depois de inúmeras tentativas de resolver o problema diretamente com o fabricante, com modificações que ajudaram apenas marginalmente no problema, a Figener foi contratada para um diagnóstico completo da caldeira. O Problema: característica químicas das cinzas favorecem o entupimento Durante a etapa inicial de pesquisa e investigação, a Figener constatou alto teor de potássio no combustível queimado, acima do valor típico para aquele tipo de biomassa. Quando tal combustível é queimado, a cinza possui Temperatura de Amolecimento – temperatura abaixo da qual a cinza pode ser considerada plenamente sólida – especialmente baixa. A baixa temperatura de amolecimento das cinzas significa que o fluxo de gases de exaustão precisa perder mais calor – logo, se resfriar mais – para que a cinza esteja sólida e possa ser facilmente arrastada. Quando isso não acontece, a cinza chega nos tubos do feixe convectivo ainda parcialmente amolecida, solidificando-se ao encostar nas paredes frias dos tubos. Com o tempo, esse material se acumula em depósitos petrificados até obstruir completamente o tubo, aumentando a pressão da caldeira, reduzindo sua eficiência e levando à parada. Figura 1: feixe de tubos entupido A solução passa a ser, portanto, encontrar formas de fazer o fluxo de gases trocar mais calor com a parede d’água da caldeira, chegando no feixe convectivo mais frio do que na condição original. Uma vez entendido o mecanismo do problema, decidiu-se pelo uso do CFD (Computational Fluid Dynamics) para testar com facilidade diferentes cenários operacionais da caldeira e identificar a condição de máxima eficiência possível e com mínimo risco de entupimento. Com essas simulações, também foi possível testar diferentes intervenções na caldeira (alterar composição da parede d’água, tamanho de determinados trechos, etc) que por outros caminhos seriam demoradas e custosas. Etapas do Estudo 1. Levantamento bibliográfico de problemas semelhantes A literatura científica é rica em determinados tipos de problema. Um bom estudo investigativo começa entendendo em que pé o conhecimento científico está sobre aquele tema, juntando publicações diferentes para compor a condição específica do estudo. 2. Modelagem da queima da biomassa e operação geral da caldeira Queima de material sólido em CFD é extremamente complexa, e muitas vezes pode sair do escopo da realidade industrial. O papel da engenharia consultiva nessas situações é modelar o problema para simplificar fenômenos excessivamente complexos, sem que haja perda de representatividade. Nessa caldeira, modelamos a queima a partir da composição dos gases de exaustão e demais propriedades do combustível. Figura: linhas de corrente no interior da caldeira Com isso criamos um modelo cuja simulação levava poucos dias, permitindo o teste de inúmeros cenários diferentes, otimizando a solução encontrada. 3. Seleção dos cenários de teste e simulações Conhecendo intimamente o mecanismo por trás do problema é possível pensar nos cenários de teste de forma inteligente. No estudo em questão, modificações que aumentem a troca térmica da caldeira foram testadas. Além disso, foi possível identificar o cenário limite de operação da caldeira para que a temperatura na saída fosse suficientemente baixa para evitar os depósitos. As modificações testadas envolveram: 4. Proposta final de solução do problema O problema em questão envolve otimização financeira, viabilidade de modificação na caldeira, e balanço do sistema como um todo. Com essas restrições o melhor caminho dificilmente é o óbvio. Se fosse possível, aumentar a área de troca sem dúvida seria o melhor caminho, mas esbarraria em dificuldades construtivas, custos muito elevados, além de problemas com o galpão onde a caldeira está. Aditivos no combustível poderiam ajudar, mas a demanda seria muito alta e os custos no longo prazo não valeriam a pena. A solução foi encontrar o balanço otimizado de ar secundário que garantisse a composição dos gases dentro do limite ambiental, mas que resfriasse suficientemente o fluxo de gases. Figura: distribuição de temperatura na seção de saída original Figura: distribuição de temperaturas na seção de saída após modificações propostas Ademais, determinou-se o ponto operacional limite da caldeira, inferior aos 30MW de projeto. Além de garantir uma operação confiável, esse estudo serviu de amparo técnico para as negociações entre o cliente e o fabricante. Impactos positivos para o cliente O estudo liderado pela Figener trouxe ganhos significativos para o cliente, indo além da solução trivial de substituição da caldeira. A análise do problema desde a composição química do combustível permitiu: Por que escolher a Figener? Com mais de 30 anos de experiência e uma equipe altamente qualificada, a Figener é especialista em análises técnicas avançadas que transformam desafios complexos em soluções práticas. Nossas ferramentas de simulação computacional e metodologias personalizadas garantem resultados precisos e confiáveis, ajudando empresas a aumentar a eficiência operacional e a sustentabilidade de seus projetos. Traga seus projetos para o próximo nível! Antes de aprovar novos layouts para sua usina, consulte a Figener! 📩 contato@figener.com.brDescubra como nossos estudos de CFD podem transformar a eficiência e a segurança de seus projetos.
CFD para estudo em leitos fluidizados: compreensão de fenômenos complexos orientam procedimentos de manutenção
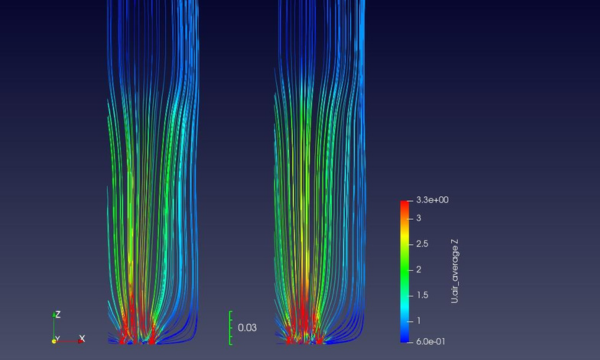
Uma grande caldeira de leito fluidizado apresentava desgaste prematuro dos tubos imersos no leito. A principal suspeita era a alteração do ângulo de injeção de ar em seu piso, juntamente com possível formação de aglomerados grosseiros de areia e nova composição do carvão queimado. Cada vez que um tubo falhava era necessário parar a caldeira, esperá-la esfriar completamente e drenar a água dos tubos evaporadores. Isso levava dias, trazendo prejuízos imensos à unidade. Alguns “escudos” de sacrifícios foram instalados, mas não foram suficientes para trazer melhora significativa. Em conversas com a equipe da Figener, o CFD (Computacional Fluid Dynamics) foi aventado como um bom caminho investigativo. Entender o mecanismo de falha e as regiões em que a erosão é favorecida traz material valioso para decidir qual caminho seguir para solucionar o problema. O Problema: aumento da erosão após alteração do ângulo de injeção de ar O mecanismo de operação de uma caldeira de leito fluidizado é bastante complexo e por vezes misterioso. O movimento do material granulado envolve efeitos contra intuitivos, que podem levar a entendimentos equivocados e, consequentemente, a soluções pouco frutíferas dos problemas. Nessa caldeira, o problema parecia ser o novo bico de injeção de ar orientado mais para cima do que o anterior. O cliente estava prestes a reverter a modificação milionária feita, por ter certeza do efeito causal do novo jato. Nas primeiras semanas de trabalho, contudo, ficou claro que a penetração do jato era mínima, e que poucos centímetros acima do piso o efeito do ângulo do jato já era dissipado e o fluxo de ar era essencialmente vertical. Figura: diferentes ângulos de jato não afetam a fluidização acima de 3cm do piso O que causava a erosão permanecia, portanto, um mistério. Etapas do Estudo 1. Modelagem do problema para torná-lo viável Simulações CFD de leito fluidizado são amplamente adotadas, mas são extremamente pesadas. Assim, na realidade industrial, é fundamental simplificar o modelo garantindo um tempo hábil de execução das simulações, mas sem perda de representatividade. Essa primeira etapa envolveu uma extensa revisão bibliográfica para amparar cada hipótese simplificadora adotada. Por exemplo, tratar de uma fatia 2D da caldeira (ao invés do conjunto 3D completo) permitiu rodar os mais de 30 casos necessários ao estudo, ampliando muito o conteúdo científico obtido com a investigação. 2. Simulações com modelos customizados de erosão Modelar a erosão é complexo, e muitas vezes não está presente nativamente nos softwares de CFD. Assim, foi necessário customizar o código para incluir modelos de erosão conforme disponíveis em publicações científicas 3. Identificação dos mecanismos de movimento do leito e de erosão Nessa etapa, analisamos cuidadosamente todos os casos iniciais rodados, identificando como o leito se comporta sob diferentes condições. Testamos, por exemplo, diferentes vazões de ar, diferentes alturas estáticas de leito, diferentes composições granulométricas do leito, etc. Figura: mapa que mostra potencial erosivo do leito, em modelo customizado Cada conjunto de casos gerava material que compunha o entendimento geral do fenômeno. 4. Análise dos casos e orientações gerais Com os mais de 30 casos rodados, a Figener descreveu com detalhes o mecanismo de erosão. Ficou claro, por exemplo, que o leito se estratifica durante a operação, e que partículas grosseiras, que se acreditava afundarem na operação, na verdade permanecem parcialmente em suspensão, acelerando significativamente o processo de erosão. Isso permitiu gerar recomendações sobre a consistência granulométrica do leito. Figura: composição média do leito estratifica diferentemente o leito, mudando distribuição de particulado grosseiro (em branco) Impactos positivos para o cliente Esse estudo de alto caráter científico trouxe um entendimento incomparável sobre o funcionamento da caldeira. Com o estudo, ficou claro que o jato de ar não é um problema, e que a solução do escudo, por exemplo, agravava o problema. Além disso, foi possível Por que escolher a Figener? Com mais de 30 anos de experiência e uma equipe altamente qualificada, a Figener é especialista em análises técnicas avançadas que transformam desafios complexos em soluções práticas. Nossas ferramentas de simulação computacional e metodologias personalizadas garantem resultados precisos e confiáveis, ajudando empresas a aumentar a eficiência operacional e a sustentabilidade de seus projetos. Traga seus projetos para o próximo nível! Antes de aprovar novos layouts para sua usina, consulte a Figener! 📩 contato@figener.com.brDescubra como nossos estudos de CFD podem transformar a eficiência e a segurança de seus projetos.
Como as simulações CFD são usadas nos mais variados segmentos industriais

Simulações CFD permitem visualizar e analisar o comportamento de fluidos em diversas situações, auxiliando na resolução de problemas complexos e na otimização de processos. Seja na redução de custos operacionais, na melhoria da eficiência energética ou no teste de novos equipamentos, o CFD oferece dados valiosos para superar desafios e alcançar resultados positivos. O que é CFD e como pode ajudar a indústria A Dinâmica dos Fluidos Computacional (CFD, da sigla em inglês) revolucionou a forma como as empresas enfrentam seus problemas de engenharia. Antigamente, as equipes dependiam de testes e experimentos físicos em seus equipamentos, o que por vezes era muito custoso, arriscado e demorado. Em problemas muito complexos, ainda, os experimentos eram inconclusivos e resultavam na substituição desnecessária de equipamentos – quando a solução poderia ser relativamente simples. Com maior acesso à capacidade computacional, as ferramentas computacionais de engenharia, dentre elas o CFD, tornaram-se progressivamente mais frequentes na indústria. Hoje em dia, o CFD é aplicável em praticamente qualquer segmento, servindo como uma ferramenta poderosa na solução de problemas e melhorias de processos industriais. O fluxo de solução do CFD envolve, inicialmente, recriar virtualmente o objeto de estudo, seja ele um equipamento, um produto, um galpão, ou até toda a unidade fabril. Cada aplicação envolverá o estudo de diferentes fenômenos físicos – como escoamentos de fluidos, transferência de calor e massa, reações químicas, etc. Esses fenômenos são modelados por meio de equações governantes inseridas no código do software e solucionadas a cada problema. Assim, por trás do software de CFD está, essencialmente, uma rotina de solução de equações que regem os fenômenos físicos pertinentes àquela aplicação. Os resultados são apresentados em 3D e permitem observar como qualquer propriedade (velocidade, temperatura, pressão, fração mássica, taxa de transferência de calor, etc) evolui em qualquer ponto do objeto, ao longo do tempo. As aplicações de simulações CFD são extremamente amplas. Pode-se, por exemplo, analisar o escoamento de ar ao redor de um avião, a formação de gases em motores, a condensação de fases em chapas frias, a dispersão de poluentes, a evolução de reações químicas em reatores, o aquecimento de um forno em sua partida, evolução de uma onda de pressão após um surto etc. Toda e qualquer aplicação física já modelada por equações pode ser, em algum grau, analisada por meio de CFD. A diversidade com que podem ser empregadas justifica a popularidade das simulações CFD como uma ferramenta poderosa de investigação de problemas complexos. Muitas indústrias de ponta realizam inúmeros ensaios virtuais em seus equipamentos para testá-los sob condições variadas e extremas, encontrando qual a configuração otimizada daquela aplicação. Ademais, problemas operacionais que muitas vezes parecem irresolúveis ganham nova perspectiva quando analisados com simulações CFD. Utilizar-se de CFD em problemas de engenharia, contudo, requer extremo cuidado. É imprescindível que seja utilizado por engenheiros com alto grau de conhecimento técnico e teórico. Justamente por resultarem em figuras e 3Ds muito chamativos e cativantes, as simulações podem frequentemente ser enviesadas e errôneas, trazendo mais prejuízo do que valor. É fundamental que o usuário entenda profundamente o fenômeno estudado, e tenha um altíssimo grau de intuição física para identificar vieses e verificar a validade dos resultados. Por solucionar inúmeros modelos e equacionamentos multilateralmente acoplados, basta pequenos descuidos para que o resultado obtido seja irreal, fruto do viés do operador na seleção dos modelos e ajustes dos parâmetros. Créditos da imagen: arquivos Figener Softwares CFD e o OpenFOAM O algoritmo por trás dos códigos CFD não é algo recente. Seu primeiro uso em software comercial data do começo dos anos 1980 e desde então diversas empresas desenvolveram suas versões em variados níveis de complexidade, biblioteca de fenômenos físicos, qualidade da interface gráfica e suporte. Nessa mesma época surgiu o projeto por trás do OpenFOAM – versão open-source do algoritmo – que hoje é um dos principais softwares disponíveis. Por ser escrito em código aberto, o OpenFOAM permite que o usuário customize o software para incluir quaisquer modelos que desejar. Por exemplo, se uma publicação científica propõe um novo jeito de se calcular determinado fenômeno físico, é possível incluir seu equacionamento no software, algo virtualmente impossível em softwares comerciais. Ademais, a ferramenta conta com milhares de usuários no mundo, criando uma comunidade ativa de ajuda mútua. Em mãos experientes, o OpenFOAM é sem dúvida uma das melhores (senão a melhor) opções para a solução de problemas complexos. Sua versatilidade e robustez, juntamente com a ampla disponibilidade de material e publicações científicas, traz uma flexibilidade ímpar, fundamental para engenheiros. Uso de CFD em projetos da Figener A Figener possui uma vasta experiência e capacidade no desenvolvimento de estudos de CFD, oferecendo soluções avançadas para diversas indústrias. Dos seus quase 35 anos de atuação, mais da metade contou com constante presença de projetos e estudos em CFD, tornando-a uma das poucas empresas brasileiras consagradas no setor. Como discutido, a capacidade técnica do usuário do software é fundamental para que os resultados sejam representativos e úteis; mais do que figuras coloridas, o interesse é trazer ganhos reais para o cliente. A Figener é composta por um corpo técnico de altíssima capacidade, com experiência em muitos setores industriais. Esse conjunto de profissionais está sempre a par de todos os projetos, contribuindo cooperativamente para entregar a melhor solução possível. Em seus estudos e diagnósticos, a Figener ajuda a identificar problemas que a equipe de engenharia local muitas vezes não conseguiu resolver. Fazendo uso de simulações em CFD, a Figener ajuda a reduzir desperdícios energéticos, reduzir custos operacionais, aumentar a vida útil dos equipamentos, realizar testes operacionais sem necessidade de parada, e testar modificações nos equipamentos sem necessidade de protótipos. Seja na geração de energia, indústrias de óleo e gás, indústrias químicas ou em setores de utilidades e de processo, há sempre um especialista da Figener focado em obter a solução ideal para aquele problema. Créditos da imagen: arquivos Figener Alguns projetos recentes realizados pela Figener envolveram análise de: Além de usos menores e pontuais para ajudar na visualização e apresentação de resultados de outros estudos e serviços. Como
Solução de Falha na Parede Refratária de Incinerador Organoclorado de Gigante Petroquímica
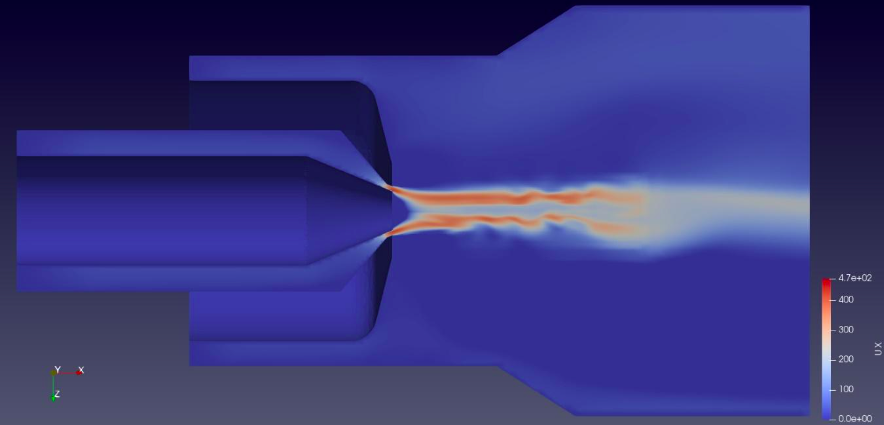
A manutenção e operação eficiente de incineradores industriais são cruciais para a segurança das operações de empresas químicas. Neste artigo, exploraremos um caso de sucesso da Figener, que solucionou falhas recorrentes nas paredes refratárias de um incinerador de organoclorados de uma das maiores petroquímicas do mundo. Através de uma investigação detalhada e estudos de Dinâmica dos Fluidos Computacional (CFD), a Figener identificou e corrigiu problemas operacionais complexos, garantindo a integridade e eficiência do equipamento. Contexto do Problema A empresa em questão, que como já destacamos é uma das principais no segmento de petroquímicas do mundo, enfrentava um desafio significativo em suas operações. Após aumentar a demanda da planta e redirecionar uma quantidade maior de organoclorados (resíduos industriais) para um incinerador existente, a empresa começou a observar falhas sérias e frequentes na parede refratária do equipamento. Julio Pieri, coordenador de projetos da Figener, explica. “A empresa aumentou a demanda da planta e passou a precisar incinerar mais organoclorados. Eles direcionaram tudo para esse incinerador existente, que tinha uma capacidade de projeto inferior à nova demanda.” Com o tempo, diversos problemas começaram a surgir, incluindo vazamento nos dutos de gases, deterioração da estrutura metálica dos equipamentos ao redor, falha no refratário e corrosão nos tubos. Inicialmente, acreditava-se que o problema estava relacionado à escolha inadequada do material refratário e seus suportes. Embora a correção desses pontos tenha ajudado, não resolveu completamente o problema. Investigação detalhada A Figener foi chamada para realizar uma consultoria geral, em que a equipe conduziu uma investigação profunda de todo o sistema de incineração, incluindo queimadores, trocadores de calor, quenches e scrubbers. Julio detalha o processo. “Levantamos inúmeros documentos, visitamos a planta algumas vezes e conversamos longamente com a operação. Ao analisar os dados, alguns problemas operacionais ficaram claros. A partir daí, levantamos hipóteses e as testamos em cálculos.“ Foram realizadas visitas e medições na planta, tanto com o equipamento em operação quanto durante uma parada programada. A equipe da Figener entrou no incinerador, analisou fotos e conversou extensivamente com a equipe de manutenção. Depois dessa extensa análise, ficou claro que o problema não era apenas na parede do refratário. “A equipe de manutenção já tinha alguma ideia do que poderia estar acontecendo. Levantamos algumas hipóteses que testamos e verificamos em modelos – sejam cálculos no Excel ou CFD“, conclui. Estudo de CFD Uma parte crucial da investigação foi o uso de Dinâmica dos Fluidos Computacional (CFD) para analisar o problema específico do refratário. Julio esclarece: “Usamos as simulações CFD para verificar uma das nossas principais hipóteses: a chama da combustão encostava no refratário bem no local de falha.“ O estudo de CFD envolveu diversas etapas e incrementos de complexidade para simular todo o forno. Inicialmente, o queimador foi isolado para extrair o comportamento do fluxo e da combustão na entrada do forno. Julio explica a importância dessa abordagem. “É fundamental tratarmos o problema em degraus de complexidade. Ou seja, começar com um problema simplificado e ir caminhando progressivamente para o problema completo. Isso porque são simulações complicadas e pesadas“, complementa o coordenador. A simulação do queimador isolado permitiu à equipe testar e investigar caminhos diferentes para chegar a um mecanismo representativo e simplificado da combustão, com destaque para o desafio devido à natureza complexa dos compostos organoclorados sendo incinerados. Esses resultados serviram como condições de contorno para a simulação de todo o incinerador, uma estratégia que economizou 70% do tamanho da malha e permitiu a execução de mais casos no mesmo período. Isso possibilitou testar diferentes cenários e aprofundar a análise do problema. Descobertas e soluções Os estudos de CFD apontaram vários problemas na operação do incinerador, incluindo: Com base nessas descobertas, a Figener fez algumas recomendações à empresa cliente. Julio Pieri detalha as principais, especificamente referente aos estudos realizados de Dinâmica dos Fluidos Computacional. “Recomendamos mudar a geometria do queimador superior (próximo à região de falha no refratário), aumentando e alargando um pouco sua pré-câmara. Com isso, a chama não entraria tanto na câmara principal do incinerador, evitando que pudesse ser fletida e encostasse na parede superior do refratário (região de falha)“, explica. Além disso, a equipe sugeriu ajustar a distribuição de resíduos entre os queimadores: “Ao invés de mandar quantidades iguais para os dois, tentar mandar um pouco mais no de baixo do que no de cima“, acrescenta. Resultados Embora as soluções ainda não tenham sido implementadas, elas se mostraram consistentes com outros problemas e hipóteses antigas que a equipe de manutenção da empresa enfrentou. As recomendações da Figener garantem resultar em uma operação mais estável e segura do incinerador, eliminando as falhas recorrentes na parede refratária e melhorando a confiabilidade do equipamento. Conclusão Este caso de sucesso demonstra a importância de uma abordagem multidisciplinar e detalhada para resolver problemas operacionais complexos em equipamentos industriais. Através de uma investigação minuciosa e do uso de tecnologias avançadas como o CFD, a Figener conseguiu identificar falhas críticas, garantindo a continuidade segura das operações da gigante do segmento petroquímico. A combinação de expertise técnica, metodologia rigorosa e tecnologia de ponta permitiu à Figener oferecer soluções personalizadas e eficazes. Quer saber como podemos ajudar sua empresa a resolver desafios de engenharia e otimizar suas operações? Entre em contato conosco para uma consulta personalizada e descubra como nossa expertise pode impulsionar a eficiência e a segurança de seus processos industriais.
Descarbonização: Chave para a Sustentabilidade no Setor Industrial e de Energia
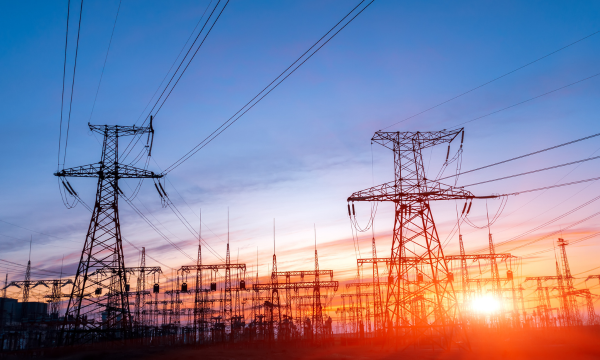
Descarbonização: Chave para a Redução de Emissões de Gases no Setor Industrial e de Energia A descarbonização deixou de ser tendência para se tornar necessidade urgente na busca por um futuro mais sustentável. Com o agravamento das mudanças climáticas, governos, empresas e sociedade civil unem esforços para reduzir as emissões de gases de efeito estufa (GEE) e mitigar os impactos ambientais.